Keeping your lubrication system running smoothly requires more than just top-quality lubricants. You also need to pay attention to the air that enters and leaves the system. In particular, you need to make sure that moisture doesn’t enter the system, which can cause corrosion and other problems. Desiccant breathers serve an important purpose in lubrication management by helping to keep contaminants like moisture and debris out of the system. However, there are a few tips and tricks that can help you get the most out of them. In this blog post, we’ll go over some of the best ways to take advantage of desiccant breathers for optimal lubrication management.
What is a Desiccant Breather?
A desiccant breather is a device that helps to keep lubricating oils free from water contamination. The breather consists of a housing filled with a desiccant material, such as silica gel, that absorbs moisture from the air. When lubricants are exposed to air, the moisture in the air can cause water contamination. This can reduce the lubricity of the oil and lead to wear on metal surfaces. The desiccant material in the breather helps to prevent this by absorbing the moisture from the air before it has a chance to contaminate the lubricant. As a result, using a desiccant breather can help to extend the life of lubricants and reduce wear on metal surfaces.
Desiccant Breather Tips for Optimal Lubrication Management
Make Sure You Have the Right Size Desiccant Breather
Your airflow rate is among the most crucial things to think about when evaluating desiccant breathers. The necessary cubic feet per minute (CFM) determines the size of the right desiccant breather. For the best results, always select a breather with a CFM capacity greater than what your tank or reservoir requires. A desiccant breather with insufficient airflow will create a buildup of pressure, resulting in a vacuum and potential equipment damage. So, the right breather will allow enough airflow to support lubricant flow inside the system. When looking at breathers, manufacturers typically provide both gallons per minute (GPM) and cubic feet per minute for your reference.
Consider Your Operating Environment
Before picking a desiccant breather, there are several things to take into account:
- What type of environment will it go in?
- What is your application of the equipment?
- What is the airflow rate, both average and maximum?
- What is the reservoir’s maximum capacity?
- Is equipment operation continuous or intermittent?
You must consider all of these operating conditions because they contribute to contamination levels. For instance, an operating environment with a lot of dirt or water spray will require a desiccant breather capable of holding high amounts of contamination. Additionally, a breather with a check valve may be necessary for harsh settings.
Check the Application of Your Desiccant Breather
There are different desiccant breathers for different applications and types of work. They come in a variety of sizes with many features, depending on the application (what kind of machinery you have or what sort of plant you’re working in). Here are some examples of typical application categories:
- Disposable Stationary Applications – Gearboxes, fluid reservoirs, transformers, pumps, and storage tanks.
- High Humidity or Dust Applications – Paper mills, wash-down rooms, steam cleaning rooms, and mine quarries.
- High Vibration Applications – Cranes, railroad maintenance vehicles, construction vehicles, and off-road trucks.
- Limited Space Applications – Gearboxes, drums, totes, and small oil containers.
- Extreme Environment Applications – Windmills, wind power turbines, mining equipment, farm equipment, and off-road vehicles.
- Caustic Fumes and Gases Applications: Forklifts, hydraulic fluid reservoirs, airport boarding jetways, and baggage haulers.
Prevent Exposure to Oil Mist
To do so, you can increase the distance between the bottom of the breather and the top of the reservoir. Attach a small length of pipe between the desiccant breather and the reservoir instead of attaching it directly. This will prevent any oil mist from coming up from the reservoir to the breather.
Know Your Reservoir Capacity
The reservoir capacity influences how quickly the desiccant is saturated. In most cases, more oil means more humidity. Also, larger reservoirs may experience more headspace fluctuation. This impacts the amount of air passing through your breather. Breathers have different reservoir capacity requirements. So, before purchasing a breather, make sure to check the model number for specifics on reservoir capacity.
Get a Desiccant Breather with a Check Valve
You can purchase a desiccant breather for either intermittent or continuous flow. Check valves play an important role in extending the life of a breather, and are generally included in breathers. This is an essential feature to consider, as it reduces the amount of air your desiccant has to filter. The silica gel will last longer when only the air that needs to be inhaled is dried. Check valves or a bladder system allows this to happen. A check valve in a desiccant breather prevents airflow into it unless the differential pressure between the atmosphere and fluid reservoir exceeds a certain level. Desiccant isolation check valves prevent the desiccant from coming into contact with exhaust air, thereby extending its life and protecting it from fumes and lubricant splashes.
Opt for More Filtration than Less
Some desiccant breather models include components that can help extend their lifespan. A carbon-filled foam filter on the bottom of the breather absorbs any oil vapor or oil splashing up. Exposure to lubricant vapor or splashes can shorten the breather’s life. Moreover, high-capacity air filters provide the best performance in extremely dusty or dirty environments. A desiccant breather must also have particle removal filters with sufficient capacity and capture efficiency. As an example, if you need a 5-micron filter for your oil, you also need the same quality filter for your breather.
Don’t Rely Solely on Silica Color Changes
Using manual indication vacuum gauges, you can see when it’s time to change your breather. Breathers working in dry conditions may not receive enough moisture to induce the silica to change color before the first particle filter becomes clogged with dirt and debris. The best way to see this when it occurs is with a vacuum gauge.
Prepare Your Desiccant Breather for Cleaning
Wash-down caps are perfect for equipment in dusty settings or that you must clean regularly, such as in mining, cement, paper, or food processing operations. These caps keep water out of the headspace and breather.
Check for Missed Openings in Your System
A very easy mistake to make when implementing desiccant breathers in your lubrication management plan is to miss openings in your system. There are frequently many egress points in sumps and vessels. However, even if your desiccant breather is perfect for your equipment and application, it doesn’t help if you install it next to other openings that don’t have the same protection.
Follow Instructions to Reuse Your Desiccant Breather
Manufacturers build many desiccant breathers with the ability to dehydrate and reuse the desiccant. You can do this by passing clean air through the breather, or by putting the desiccant in an oven for a few hours. As long as there isn’t any oil buildup on the silica gel granules, you may be able to reuse the desiccant three to five times. However, always check the instructions for your desiccant breather for guidance on reusability.
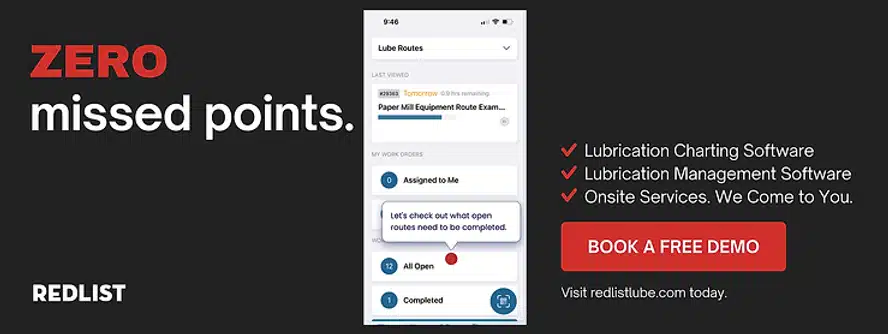
The Key to Extending Equipment Life
Proper lubrication management is key to the longevity of your equipment. By following these simple desiccant breather tips, you can ensure that your machinery runs smoothly for years to come. If you have any questions about how to apply these principles or need help with your lubrication management strategy, don’t hesitate to contact us. We’re here to help you get the most out of your lubrication management program.