Root cause analysis, or RCA, is an intimidating and often underutilized method of analysis. Recently, however, the use of RCA in asset maintenance is gaining popularity. Most reliability professionals turn to RCA to decode lubrication failures and from there devise the ideal maintenance steps to reduce future failures.
Reliability experts who advocate for the use of root cause analysis believe that there is a lot more to learn from machine failures than successes. After all, success is a failure that is simply waiting to happen. Understanding the hows and whys of an asset failure provides a foundation for an effective and efficient maintenance strategy. This post provides an in-depth look into root cause analysis and how to use it to understand lubrication failures.
What is Root Cause Analysis?
RCA is a systematic method that seeks to identify and record all the possible causes of a problem. Performing an RCA can be beneficial for any industry, but it is especially valuable in manufacturing, information technology (IT), healthcare, engineering, and scientific research.
In asset maintenance and lubrication, RCA starts when an asset fails. The maintenance team performs RCA by looking at the steps or events that led to the failure. Through this process, the team repetitively asks the reason for each step or event leading to failure. Thus, some also refer to RCA as the process of “Asking the Repetitive Whys” or the “Five Whys.” The initial whys reveal the immediate or obvious causes of the failure. Further, asking the whys of these causes should reveal other contributing factors that could lead to the root cause of the failure.
However, zeroing in on the root cause of machine and lubrication failure is not that simple. The process could result in multiple causes that the maintenance team must evaluate according to their possibility and relevance. Creating fishbone diagrams, also called Ishikawa diagrams, is often useful to guide in the process of evaluating and eliminating these possible causes.
To perform root cause analysis and gain critical failure insights, you and your team must have the necessary technical knowledge, experience, and skill. Otherwise, any attempt at doing an RCA will be an endless and unfruitful one. You can also take additional steps to ensure the success of RCA, such as reviewing historical records of similar failures, performing a fault tree analysis (FTA), utilizing troubleshooting guides, and seeking the services of machine and lubrication failure experts.
Decoding Lubrication Failures
Root cause analysis gets more complex when performed to analyze lubrication failures. Most industries utilizing heavy equipment and similar assets encounter lubrication problems. But, machine failures due to lubrication problems are often mistaken to be caused by other factors.
In addition, most facilities often accept that poor lubricants or lubrication practices are normal. Because lubrication is seldom considered a potential cause of machine failure, most facilities miss out on the opportunity to gain significant benefits to their bottom line. And this is at the minimal expense or investment of improving lubrication.
Root Cause Analysis Process
There are several ways to approach a root cause analysis, but below are the general five phases involved in the process:
1. Data Collection
At this phase, the maintenance team collects information immediately after a failure occurs. Valuable data and physical evidence can come from evaluating the lubricants, filters and separators, deposits or by-products of chemical reactions, and other areas. The areas of data collection can be as wide or as specific depending on the asset failure history, critical failure points, and unique usage of the machine.
2. Assessment to Determine the Root Cause
This phase involves the analysis of collected data to identify the cause of failure. The first step is to identify the problem and its significance. Then, the investigators must work backward until the root cause is identified. Here, having the knowledge and expertise in the main types of lubrication-related failures comes in handy. These lubrication failure types will be briefly discussed in the following sections.
3. Identification of Corrective Actions
The RCA process must produce corrective actions that will improve machine reliability and safety. Corrective actions must prevent future failure from recurring, but must also be practical, aligned with the company’s goals, and not pose additional failure or safety risks. Identifying corrective actions requires in-depth consideration of the consequences of implementing or not implementing the proposed corrective actions.
4. Information Dissemination
During this phase, the corrective action implementation takes effect. The maintenance department informs all parties involved in implementing the corrective actions. All the affected units or teams must know the purpose and expected results of such actions on their current processes. Information must also be released to affected external parties such as suppliers, contractors, and related service providers.
5. Following Up
Follow-ups ensure that corrective actions were implemented properly, and are achieving their intended purpose of fixing the lubrication problems. Recurrence of problems may happen and thus, the corrective actions must be reevaluated, discontinued, or revised.
Lubrication Failure Types You May Uncover with Root Cause Analysis
Below are the main lubrication-related failures considered when performing root cause analysis:
Lubricant Volume
When the volume of lubricants used is excessive or insufficient, it can result in lubrication-related machine failures. Excessive lubricant is a common issue in manually applied lubricants, over-greasing of bearings, for example. Automatic lubrication systems seldom cause over-lubrication, but these systems can malfunction and deliver more than the necessary lubricant.
Insufficient lubricant volume often happens due to missed relubrication schedules. Minimal loss of lubricant is normal. And this loss must be replenished regularly to prevent failure. But a sudden and significant drop in lubrication levels can result from leaking lubricant, inaccessible lubrication points, or failure of the delivery system.
Wrong Lubricant
Using the wrong lubricant is a common problem and can come from various sources, including the lubricant, lubrication process, human error or lack of training, machine design, management, and other external factors.
Specific common reasons include inappropriate or low-quality lubricant, mislabelling of lubricant or machine parts, wrong work order instructions, errors in following usage directions, exposure to contaminants, and incompatible initial and replenishing lubricants.
Contaminated Lubricant
The use of contaminated lubricant is as harmful to machines as using the wrong lubricant. Contaminants cause machine wear and failure by changing the lubricant’s physical, chemical, and performance properties. Contamination happens due to:
- Inadequate measures to exclude contaminants, such as tampered seals and open containers, contaminated transfer pipes or hoses, exposure of vent breather to dirt and water spray, etc.
- Ineffective measures to remove contaminants.
- Insufficient resistance to contaminants, which happens when lubricants react with contaminants and produce more contaminants in the process.
Lubricant Failure
Lubricants naturally wear out and degrade, decreasing performance over time. Early degradation, however, can be a result of:
- Base Oil Failure – Base oil is the main component of lubricants. The base oil can degrade easily in high temperatures, exposure to incompatible chemicals, and mishandling.
- Additive Failure – The performance of additives starts degrading as soon as the lubricants are made. But additives degrade faster through poor storage and handling.
- Thickener Failure – The type of thickener used can also affect lubricant failure. High temperatures and prolonged storage can cause thickeners to separate and cause lubrication viscosity issues. To learn about the importance of maintaining lubricant quality in industrial operations, join our webinar on “Ensuring Lubricant Quality Through Effective Storage and Handling” today.
Wear Debris Generation
Analysis of debris from the wearing of machines can provide valuable insight into the state of lubrication. Abnormal debris generation can indicate lubrication problems that will eventually lead to machine failure.
Debris can be extracted from the lubricant, the filter of the lubrication system, etc. Common wear debris analysis includes atomic emission spectroscopy, ferrous density analysis, and optical microscopy. Failure investigations, however, may require additional tests such as specialized X-ray fluorescence spectroscopy, scanning electron microscopy, X-ray crystallography, and other detailed metallurgical tests.
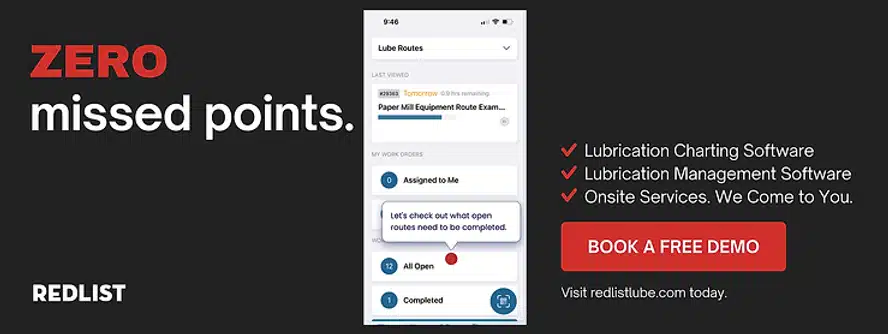
Digital Tools for Root Cause Analysis
A complex process of decoding lubrication failures through root cause analysis can gather valuable benefits from digitization. Through Redlist’s Lubrication Management Software, asset failure data can be recorded, organized, and stored conveniently. Redlist also comes with powerful computing capabilities and intelligent functions that enable faster and more accurate data analysis. Additionally, Redlist supports the evaluation and improvement of lubrication strategies based on RCA results. Redlist can provide many more benefits to your lubrication management program, schedule your free demo to learn more!