Using spreadsheets to manage your maintenance and facilities operations is significantly more expensive than you may realize. Many companies start by using spreadsheets to manage maintenance because spreadsheets are readily available as a standard component of computer software.
However, as your organization grows, your spreadsheets struggle to keep up. It takes more time and manual effort, making them a poor fit for handling the complex requirements of a developing or large organization. Switching to a modern CMMS (Computerized Maintenance Management System) automates and streamlines processes, allowing businesses to optimize their maintenance operations.
What is a CMMS?
A CMMS, or computerized maintenance management system, is a software program that you can use to manage and track maintenance activities for equipment, facilities, and other assets. It typically includes features such as work order management, inventory tracking, and preventive maintenance scheduling. The primary purpose of a CMMS is to improve the overall efficiency and effectiveness of maintenance operations by providing managers with real-time data and analytics. Organizations that manage their maintenance operations with CMMS software can ultimately boost asset productivity, cut costs, and simplify procedures.
Spreadsheets vs. CMMS: A 10-Point Performance Comparison
1. Functionality
Spreadsheets are renowned for their ability to execute complicated computations and analyses that would otherwise be difficult to perform. Yet, in contrast to CMMS software, spreadsheets have numerous drawbacks.
Maintenance management software is capable of more intricate tasks. A CMMS includes applications that:
- Track labor productivity
- Generate work orders
- Submit orders for supplies and parts
- Help determine practical times to plan routine maintenance
- Properly plan the allocation of technicians
- Aid in equipment replacement decisions
Utilizing maintenance management software leads to quicker outcomes, which boosts productivity and offers superior analytics for decision-making.
2. Accessibility
While spreadsheets are readily available, they are not widely and easily accessible. Generally, one or two employees have access to and maintain the spreadsheet. This leaves the rest of the team in the dark and requires extra steps to access or update valuable information. Alternatively, CMMS software comes in both an app for mobile devices and as a web-based, browser-accessible platform. This allows your team to access information at any time from a computer, smartphone, or mobile device.
3. Preventive Maintenance
Keeping all equipment and asset information in a spreadsheet requires searching through hundreds of entries to locate the most accurate data. Someone must physically arrange and manage resources, as well as remember when things are scheduled, to perform preventive maintenance (PM).
With a CMMS, all the data on work histories, equipment, and more are organized and kept in one place. The preventive maintenance module provides technicians with quick access to all the work orders they need to complete their PMs. It will even send notifications and reminders when the inspection or job is approaching. Additionally, you can follow work orders through the process from beginning to end. This provides access to data and trends that reveal operational downtime, repair costs, and the root causes of problems.
4. Managing Work Orders
Organizations with limited resources should avoid using spreadsheets for work order management. A spreadsheet-based system’s absence of automatic work order generation is one of its worst shortcomings. This can be especially problematic when administering a preventive maintenance program. Instead, a CMMS can create PM work orders automatically based on a predetermined timetable. Assignment, work order creation, scheduling, and distribution are very time-consuming and manual activities when using spreadsheets.
5. Inventory Management and Spare Parts Tracking
A major contributor to excessive downtime is waiting for spare parts to arrive to finish the repair. With spreadsheets, inventory management is manually documented, requiring someone to physically search for the part or place an order, which may or may not arrive on time. Then there may be additional fees to expedite the order or overnight shipping. All of this is in addition to the cost of downtime while your equipment and employees have to wait for the part.
The inventory management section of CMMS software allows you to keep track of all spare parts and necessary materials. You can examine which replacement parts are needed and order them in advance, ensuring that you always have them on hand. In some inventory management modules, you can set inventory levels to activate alerts when they reach a certain threshold, indicating that it is time to reorder. No need for a technician to travel to another location or the store to obtain the necessary parts.
6. Automation and Real-Time Information
The largest downside of spreadsheets when you compare them to a CMMS is that spreadsheets require manual data entry. This creates a bottleneck in your processes, as one or two people can enter the data. Additionally, if you pull a report without taking the time to enter all the latest data, then you are not working with real-time information. Whereas, maintenance management software allows your team to record data as they complete inspections or work orders. This keeps your insight and reporting running on real-time data. Anyone with access can log in at any time to view the most recent schedule, data, inventory, equipment performance, and other maintenance information recorded in the CMMS.
7. Centralized System
Spreadsheets require the cumbersome task of trying to manage multiple versions and multiple sources of information. To get the data you need, you may have to go in and out of several different documents or platforms. A CMMS saves you all of that time spent looking for info, as it provides one centralized location for all maintenance and asset-related tasks.
8. Analysis and Reports
Spreadsheet reports and analysis require additional manual processes to extract the data. Even then, you must take additional actions to present the data in an easy-to-read and understandable way. Alternatively, with a CMMS, you can have full reports with one click on your reporting dashboard. The maintenance management software gathers and produces all of your relevant data into a thorough report whenever you need one.
9. Integration with Other Software and Systems
Spreadsheets cannot be integrated with other programs since they are not web-based. The flexibility of maintenance management software to interact with other software systems is one of its appealing qualities. For maintenance managers who wish to further automate their processes and raise the standard of the services they deliver, system integration opens up new possibilities.
The Bottom Line on Ditching Spreadsheets for a CMMS
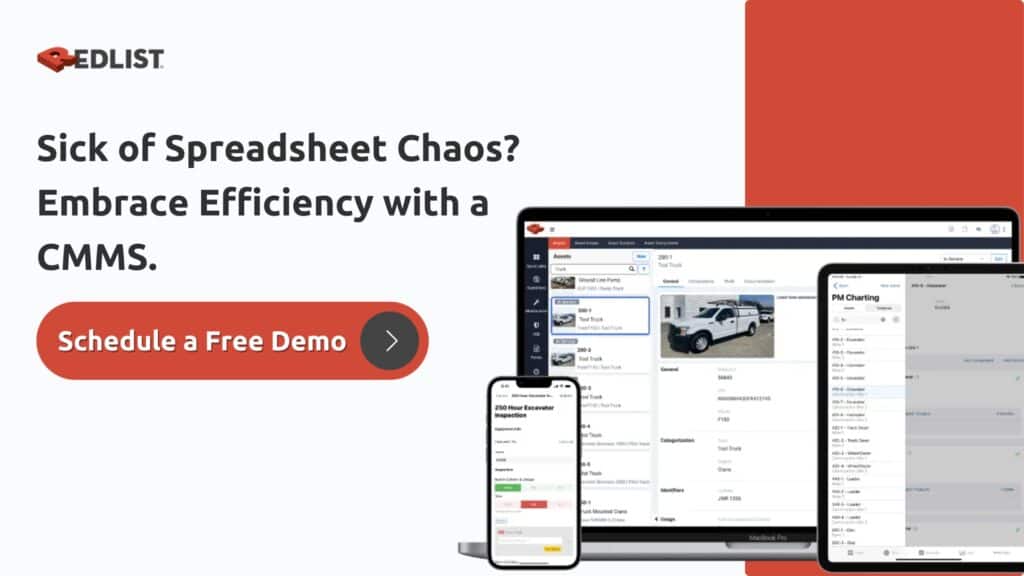
Today, we live in a fast-moving and competitive world. Companies must discover the most inexpensive, efficient, and profitable means of expanding their operations and increasing their profits. Gone are the days when a simple spreadsheet is sufficient for a maintenance manager and their team. Maintaining the accuracy of the data in a spreadsheet becomes exceedingly problematic as an organization’s assets and services continue to expand. You must switch to a CMMS maintenance software to effectively manage your maintenance operations and ultimately increase asset productivity, reduce costs and downtime, and streamline processes. To see how a CMMS can work for you, schedule a demo with a Redlist team member today.