Heavy machines and equipment come with hefty price tags. Thus, it is only natural to want to get the most out of these machines. Heavy machine maintenance aims to promote asset health and high performance and extend service life. Read on for our 9 tips to help you achieve these performance and reliability goals!
9 Tips to Optimize Heavy Machine Maintenance
Tip 1: Have a Maintenance Strategy
Establish an easy-to-execute yet effective heavy machine maintenance program and commit to it. For healthy and long-lasting heavy machines, having a maintenance strategy that suits your processes and current practices is critical. Otherwise, you will fail to sustain your heavy machine maintenance and accomplish your goal of extending the life of your machines.
A maintenance strategy should include preventive maintenance (PM) and corrective maintenance (CM). PM proactively treats machinery issues, thus preventing major and costly breakdowns. CM deals with unplanned failures and handles unavoidable malfunctions with minimal downtime.
Tip 2: Hire Trained Operators
Hiring certified and well-trained operators can cost extra in terms of salary or training, but they can save you money in the long run. You can rely on knowledgeable and experienced operators to properly and carefully use heavy machines. Experienced operators are also sensitive to early signs of machinery failure, and thus can assist in executing PM and CM programs.
Even experienced operators need regular training to refresh their knowledge of machine guidelines, regulations, and specifications. Conduct regular training for operators and their assistants to refresh and update their knowledge of heavy machines.
Tip 3: Follow Manufacturer Specifications
Machine manufacturers test their machines rigorously to establish set limits or specifications. Ignoring and exceeding these performance specifications result in machine damage and safety risks for operators and individuals around them.
Keep manufacturer specifications for reference and request updates from your supplier if available. Review these specifications regularly and refer to them whenever conducting electronic or mechanical repairs and servicing.
Tip 4: Develop a Maintenance Checklist for Operators
The operator’s main responsibility is to deliver outputs using heavy machines. However, they can also perform minor maintenance for these machines. By creating heavy machine maintenance checklists for operators, you can easily monitor the health and performance of your machines. This way, you get regular insight into your machine’s performance without the extra technical labor or material costs.
Develop maintenance checklists that are machine-specific and easy to accomplish. You don’t want your operator spending too much time on these checklists and decreasing their productivity. Over-complicated and lengthy checklists can cause operators to forego the actual inspection, thus filling up forms only for compliance.
Tip 5: Perform Regular Condition Monitoring
Regular condition monitoring aims to check for wear and tear, loose or faulty parts, cracks, and other early indicators of failure or breakdown. You can perform regular condition monitoring weekly, monthly, or annually depending on the criticality of the machine or machine parts.
Alternatively, you can hire third-party services to perform condition monitoring on top of your regular inspections. If possible, take advantage of condition monitoring tools that use advanced technologies. They can be expensive, but you can think of them as physical checkups for your machines that prevent more expensive breakdowns in the future.
Tip 6: Take Extra Care When Working in Extreme Conditions
Most heavy machines are built for extreme heat or freezing temperatures, but subjecting them to such constant abuse can significantly decrease their lifespan. Taking extra precautions under these extreme conditions will make a big difference in optimizing machine performance and lifespan.
Refer to the manufacturer’s recommendations when using heavy machines under extreme conditions. Consider the manufacturer’s precautions and train all operators to follow these precautions. If extreme conditions are unavoidable, increase the frequency of inspections and condition monitoring for better protection against malfunctions and breakdowns.
Tip 7: Keep Detailed Records of Servicing or Repairs
Proper documentation of heavy machine maintenance is critical for sustainable and efficient results. If you keep detailed records of past servicing or repairs on your heavy machines, you can focus your inspection or monitoring on critical machine parts or components. Also, you can save time and other resources because you have a reference point for all your repairs and servicing.
Digitize your records to prevent loss and misfiling. A digital CMMS (computerized maintenance management system) also makes these records accessible, further saving you time in searching for them. Accessible and updated records mean faster repairs or servicing and consequently, reduced downtime.
Tip 8: Maintain Good Housekeeping Practices
Good housekeeping practices involve cleaning and storing heavy machines after use and preparing them for the next shift’s use. Cleaning off the debris, sludge, and caked solids after use prevents contamination of sensitive machine parts. Proper storage also keeps the elements from causing damage and promoting contamination to your machines.
Proper execution of good housekeeping practices can make a significant difference in the performance and longevity of machines. You must establish proper dismantling and cleaning of your machines. Train operators thoroughly on these methods to ensure they understand the criticality of following them.
Tip 9: Prioritize Regular and Proper Lubrication
Proper and effective lubrication protects machine parts from friction, and the resulting wear and tear. Lubrication requires regular inspection and monitoring to check the effectiveness and prevent contamination buildup, which can promote faster deterioration of lubricated parts.
It is vital that you establish standard operating procedures (SOPs) for lubrication methods. By standardizing these methods, you prevent inadequate or excessive lubrication that can harm machine parts. Include inspection and monitoring protocols in lubrication SOPs to further protect lubricated parts from damage.
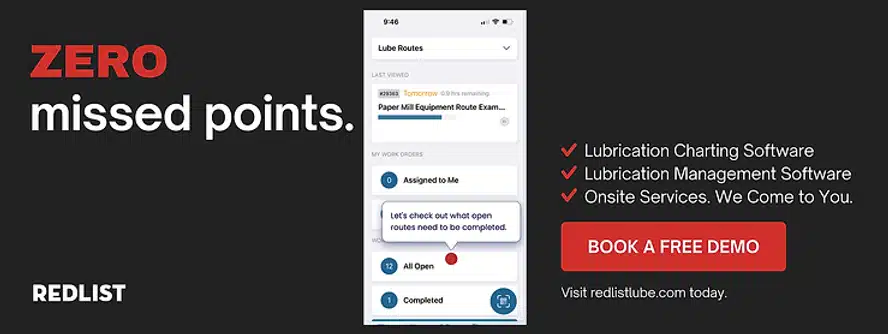
CMMS for Heavy Machine Maintenance
Heavy machine maintenance is essential for maintaining machine performance and prolonging service life. But, heavy machine maintenance can get complicated. You need all the support you can get to ensure its success. One of these valuable tools is a CMMS. Redlist’s CMMS is specifically designed software to help manage and perform maintenance procedures for faster and more accurate results. For more info on this all-in-one heavy machine maintenance tool, schedule a free demo today!