If you’re struggling with inventory management, a computerized maintenance management system or CMMS may be your solution. But before we get into the valuable benefits of CMMS inventory management, let’s define the terms.
What is a CMMS?
From its name, it is a software system that centralizes information on everything maintenance related. A CMMS is unique to every facility, serving as the database that organizes all information for its users.
CMMS Inventory Management
Inventory management is an essential area of maintenance management involved in keeping stocks of spare parts, repair tools, and other maintenance inventory. Effective inventory management ensures that materials, tools, and workforce are always available for maintenance checks and repairs whenever needed.
Before CMMS, most companies manually track inventory with paper or spreadsheets. These may be enough to get by in the beginning, but they leave room for error and bottlenecks in your inventory management. CMMS inventory management provides real-time, accessible, and more accurate information.
The 5 Essential Benefits of Using a CMMS for Inventory Management
1. Reduced Costs and Equipment Downtime
Maintenance is a costly but necessary component of every operation. CMMS provides data and trends that will allow your facility to make more informed decisions about the purchasing of inventory, maintenance of equipment, and management of vendors. In addition, maintaining precise supply records per location enables maintenance teams to minimize overstocking and out-of-stock circumstances, enhancing overall operations and budgetary projections.
Furthermore, an effective CMMS can significantly reduce equipment downtime by keeping track of the whereabouts of spare parts and notifying you when supplies are running short. The unavailability of equipment wastes time and money in several ways. For one, not knowing whether or not parts are in stock perpetuates facility failures. And, prolonged shutdowns mean less productivity and high costs. Also, you spend time and resources locating necessary items.
With effective CMMS inventory management, maintenance costs are reduced by effectively preventing equipment failures, eliminating downtime, controlling labor costs, and minimizing rushed purchases of replacement components.
2. Accurate Data for Long-Term Planning
Without accurate and timely data, determining when to order products can be a challenging component of inventory management. CMMS inventory management makes planning maintenance and restocking necessary products easier. Through CMMS, maintenance managers can access information such as preventive maintenance procedures. From this information, they can determine when and which equipment needs servicing, thus, can easily plan the procurement of the necessary resources.
Additionally, a CMMS provides insights that aid in the long-term planning of facilities. With an updated database through CMMS, managers use real-time and accurate information. Thus, you eliminate errors from time-consuming guess-and-check steps or unreliable projections.
Furthermore, stockroom managers can analyze item activity to have a deeper understanding of the supply and demand dynamics. This ultimately results in efficient and optimized purchase planning that saves costs while providing high-quality inventory.
3. Multiple Locations Using One Centralized Database
With its centralized cloud-based information system, a CMMS makes maintenance data available from any computer or mobile device at any time and location. Through the CMMS platform interface, users may readily access information regardless of the location of the inventory. In addition, information is updated in real-time, so there is no need to speculate about the availability of parts or materials or their location.
4. Inventory Control
Effective inventory management means being in control of having the required stock and amount at the appropriate time, location, and cost. A CMMS provides this control by assuring the efficient running of your stockroom and warehouse facilities.
In addition, a CMMS allows users to monitor inventory trends and determine the minimum and maximum stock levels, as well as to manage vendor costs and automate activities. This knowledge and these tools are valuable in reducing wasteful expenses and enhancing productivity.
5. Inventory Automation
A CMMS can also be configured to send prompts when stock reordering is necessary, relieving stockroom managers from the stress of reordering. Even better, a CMMS can automatically issue purchase orders for your vendors to replenish your stockroom when the minimum quantity on hand is met. In addition, a CMMS can manage the task of returning materials to supplies if needed and track the returns or changes in the stock levels accordingly.
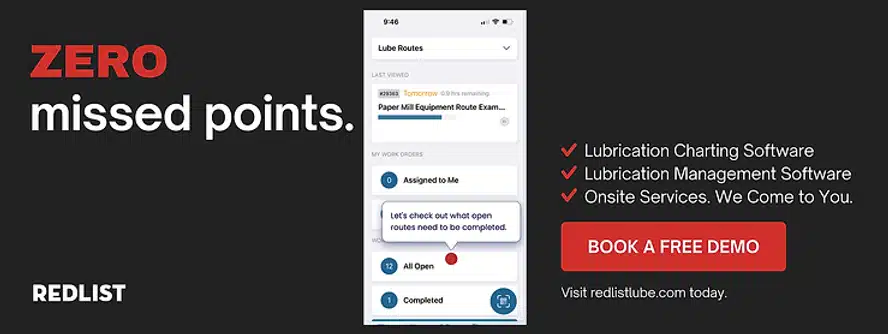
Digitize Inventory Management with CMMS
Nothing says ‘digital age’ more than a CMMS-run facility. And there’s no better way to take advantage of the digital age than by getting faster access to accurate information. Hence, your facility can perform at the top of its game and maintain competitiveness through a computerized maintenance management system. A CMMS software like Redlist helps you say goodbye to manually counting each item and making spreadsheets and notes to manage stock and spare parts. Click here to request a CMMS inventory management demo today.