Maintaining maximum productivity in the fast-paced industrial world today depends on effective maintenance management. Nonetheless, there are a few typical errors that can cause needless machine downtime, which would reduce profitability and production. We examine these common maintenance mistakes in this post and offer helpful advice on how to prevent them.
Redlist, a software that provides complete lubrication management solutions, is one simple approach to simplify maintenance procedures. Through identification and mitigation of these typical hazards, you may guarantee more seamless operations and reduce downtime.
5 Common Maintenance Mistakes Resulting to Machine Downtime
Many businesses deal with persistent problems that cause needless downtime and decreased output. Engineers and maintenance managers frequently come across a variety of typical errors that, despite their seeming insignificance, can have a big impact on the business as a whole. The first step in reducing these typical mistakes is to understand them.
Equipment breakdowns and unscheduled stoppages are caused by a variety of errors, including improper lubrication management, a failure to anticipate equipment failures, a disregard for the significance of thorough record-keeping, a lack of people training, and a failure to standardize operations.
It takes deliberate effort to get machines operating at peak efficiency. To guarantee that maintenance procedures are carried out perfectly, deliberate actions, the right equipment, and a keen eye for detail are needed. Let’s examine these typical problems and learn how to prevent them to maintain the smoothness and efficiency of your business operations.
The following are some examples of the typical errors in the maintenance sector.
1. Inadequate Management of Lubrication
The issue:
Although many firms fail to maintain adequate lubrication management, lubrication is essential for machinery to work at its best. Unreliable lubrication schedules, incorrect lubricant selection, or inability to oil important components can cause early wear, equipment malfunctions, and eventually downtime.
Resolution:
Put in place a careful lubrication management program. Here’s how to do it:
– Create a Lubrication Schedule: Create a regular timetable for lubrication tasks. This guarantees that no step is missed and helps to keep a habit.
– Select the Correct Lubricant: Various equipment and parts call for particular kinds of lubricants. Make sure the right lubricant is applied for the job at hand.
– Train Staff: Ensure that all maintenance staff members have received lubricant management principles training.
– Use software such as Redlist: which provides complete Lube Management solutions. Redlist offers automated reminders, guidance on the right lubricant types for various purposes, and assistance in keeping track of lubrication schedules. This guarantees careful and reliable lubricant control.
2. Ignoring Maintenance Predictive
The issue:
Reactive maintenance, which addresses problems only after they arise, can result in costly repairs and significant unplanned machine downtime. Predictive maintenance is a common, yet preventable, error that occurs when problems with equipment are ignored before they become serious.
Resolution:
Your maintenance strategy should incorporate predictive maintenance techniques. Here’s how to do it:
– Conduct Routine Inspections: Routine equipment inspections can assist in identifying problems before they become more serious.
– Adopt Predictive Technologies: Use technologies to keep an eye on the condition of machinery, such as vibration analysis, thermography, and oil analysis.
– Analyze Data: Monitor equipment performance data to spot patterns and anticipate malfunctions.
– Use Software: Redlist and other programs can help you forecast when maintenance needs to be done by using sophisticated algorithms and gathered data.
Learn how Redlist’s predictive features can assist you in preventing unforeseen outages. For a free demo of the software, schedule one.
3. Lack in Record-Keeping and Documentation
Issue:
It can seriously impair your ability to properly maintain machinery if you keep insufficient records or forget to document maintenance actions. It is hard to keep track of what has been done, spot reoccurring lubrication issues, or adhere to legal obligations when there is little documentation.
Resolution:
Invest in a reliable mechanism for keeping records. Here’s how to do it:
– Use Digital Records: Keep digital records of every maintenance procedure. Paper records are prone to damage or loss.
– Standardize Documentation: Make checklists and forms that are the same for all maintenance jobs.
– Train Staff: Make sure that every employee knows the value of keeping accurate records and is conscientious about keeping them.
– Centralize Data: For maintenance management, use centralized software. Redlist makes it simple to obtain and analyze data as needed by organizing and managing all of your maintenance records in one location.
Schedule a Free Demo:
Are you sick of messy maintenance records? Check out how Redlist can make the process of documenting easier. Book a free demo now.
4. Inadequate Maintenance Personnel Training
The issue:
Inadequate training can lead to inaccurate maintenance procedures, inappropriate handling of equipment, and ultimately, more downtime. Insufficient expertise among employees may result in frequent malfunctions and reduced output.
Solution:
Make sure your maintenance personnel receive ongoing training and development. Here’s how to do it:
– Conduct Regular Training: Provide staff with regular training sessions to be informed about new technology, safety procedures, and best practices.
– Credentials and Courses: Encourage employees to enrol in specialist courses and earn the necessary credentials.
– Cross-Training: To guarantee operational flexibility and coverage, train numerous personnel on various pieces of equipment.
– Make Use of Technology: Redlist may assist by offering guidelines and training materials within the platform, making sure that every member of your staff is knowledgeable about the best practices for lubrication management.
Do you want your team to be the greatest in the industry? Give them the information they require by using Redlist. Schedule a free demo to find out more.
5. Inability to Adopt Standardized Protocols
The issue:
Inconsistent practices and uneven maintenance quality can arise from the lack of standardized maintenance methods, which can lead to frequent equipment breakdowns and unscheduled machine downtime.
Resolution:
Create and codify maintenance protocols. Here’s how to do it:
– Create Standard Operating Procedures (SOPs): Write succinct, understandable SOPs for every maintenance task.
– Regular Updates: Update SOPs on a regular basis to reflect new developments in technology and expertise.
– Training: Make certain that every employee receives this standardized procedural training.
– Monitoring and Compliance: Make use of instruments to keep an eye on SOP adherence. Redlist may track adherence to established protocols and send out reminders to maintain consistent maintenance quality.
Increasing Maintenance Effectiveness and Decreased Machine Downtime with Redlist
Redlist proves to be an effective tool in addressing various maintenance obstacles, as it is specifically made to optimize maintenance procedures and minimize needless machine downtime. This program provides an integrated suite of solutions to improve operational efficiency by addressing and mitigating all the common maintenance errors that we identified in our article.
Lubricant Management:
Redlist is an excellent lubrication management solution since it offers a complete platform for planning and monitoring lubrication tasks. To make sure nothing is forgotten, users can create comprehensive lubrication schedules that are specific to each piece of equipment. Maintenance staff are kept on task by automated alerts and reminders, and the integrated database facilitates the proper lubricant selection for certain pieces of equipment. Longer equipment life and fewer malfunctions are the results of this careful approach to lubrication management.
Predictive Maintenance:
Redlist’s sophisticated analytics capabilities make predictive maintenance less intimidating. The software uses information from oil analysis and routine inspections to forecast when equipment may break. With the help of these predictive insights, maintenance personnel can take proactive measures to resolve possible issues before they become more serious ones. This forethought lowers the need for expensive emergency repairs and unplanned downtime.
Maintaining Records and Documentation:
Redlist centralizes all maintenance logs in a digital format, making record-keeping easier. It is simple to track trends, record every maintenance action, and adhere to legal obligations with the help of this consolidated repository. The highly navigable interface of the platform guarantees that maintenance records are readily available and intelligible, facilitating prompt decision-making and the examination of previous data.
Education and Uniformity:
Redlist facilitates ongoing employee training by offering guidelines and tools on the platform. Additionally, it supports the creation and implementation of standard operating procedures (SOPs) for maintenance-related tasks. Redlist contributes to the preservation of a high and consistent standard of work by making sure that all staff members are trained and that protocols are regularly followed.
Redlist is an essential component of any maintenance plan. Redlist optimizes maintenance activities and ensures a more dependable and efficient operation by addressing the underlying causes of needless downtime, such as inadequate lubrication management, a lack of predictive maintenance, poor documentation, inadequate training, and the absence of standardized procedures.
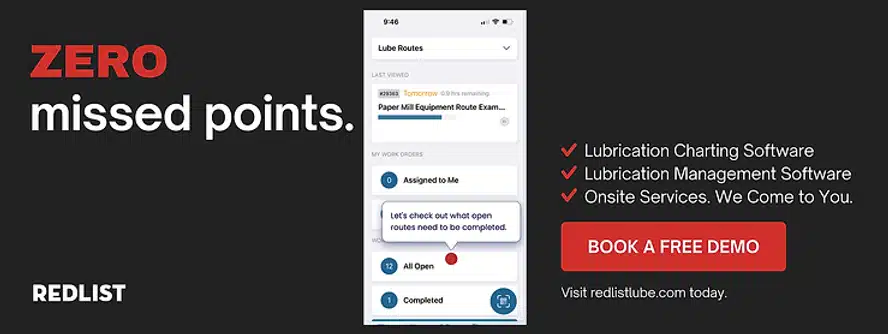
Conclusion
Repetitive downtime can be extremely detrimental to profitability and production, but it can be considerably reduced by avoiding common maintenance errors. To keep your operations operating smoothly, put your attention on predictive maintenance, consistent procedures, proper training, complete paperwork, and good lubricant management. Redlist and other similar systems can be used to further streamline these procedures, providing a comprehensive solution to uphold uniformity and high standards.
Don’t allow typical maintenance errors to hinder your output. Act now with initiative. Do you want to maximize the efficiency of your maintenance tasks? Schedule a free demo now to see the difference.