There’s no denying that equipment reliability is critical to the success of any business. When your machines are up and running, you’re able to produce products or provide services, which in turn generates revenue. Poor equipment reliability can have a major impact on your business. Not only does it lead to interrupted production and lost revenue, but it also increases your maintenance costs.
However, the challenges that many maintenance teams are facing today involve a shortage of people, a shortage of budget, and a shortage of supplies. So, what can you do to improve equipment reliability without requiring more budget or a bigger team? In this post, we’ll share some easy reliability improvement tips that you can implement starting today.
Our Top 10 Equipment Reliability Improvement Tips
Put Your Data to Work
The most successful maintenance teams are aware that data is the basis for wise business choices. It’s not sufficient to simply claim that a machine or a pump needs a replacement; you now need to provide evidence of that claim. How frequently has it failed? How much have you spent fixing the equipment over the past two years? What were the product losses to the company with the downtime? The statistics should demonstrate this clearly if this machine is indeed unreliable, and you should also compare it to other assets of a similar type.
Record Accurate Data
In order to put your data to work for you, it needs to be accurate. Maintaining a good maintenance history is the responsibility of maintenance technicians. Technicians, after all, are the ones who do the hands-on work. Nevertheless, the work does not end there. You need to accurately track preventive maintenance, repair tasks, and failures. Maintenance technicians who wish to make a difference in the equipment reliability on their site must accurately record what they do, including:
- What is the equipment ID and location of what you worked on?
- How long did the task take?
- What are the possible cause or causes of the issue?
- Were the required parts in stock and available?
Perform Root Cause Analysis
Once you have established that a particular asset lacks reliability, you should investigate the root cause. Then, take steps to either resolve or minimize the root cause. The good thing about root cause analysis (RCA) is that it requires a very low investment in training and tools. It’s critical to keep in mind that almost every failure mode might have several reasons, so keep looking and pinpoint as many causes as you can once you believe you’ve located “the cause.”
Look for Small Ways to Relieve Equipment Stress
A quick walk around your facility looking for pipe stress also requires very little investment in training and tools. Pipe stress is an incredibly common failure mode that greatly impacts equipment reliability. It is a result of inadequately supported or placed pipe flanges or fittings. Stress at pump connections can cause leaks, as well as early pump bearing and seal failures. Identify points of pipe stress due to poor fit or support in your facility, and start repairing those points right away to improve equipment reliability.
Check on Your Lubrication Practices
Lubrication issues are a major cause of equipment failure. With lubrication now so specialized, someone who learns the basics may not have enough impact to directly improve equipment reliability in one day. However, learning sound lubrication practices and standards certainly won’t hurt your equipment reliability. The learning process will reveal the flaws in your present lubrication program and what actions you can take to achieve excellence in lubrication at your facility.
Implement Condition Monitoring
Temperature, vibration, and lubrication are three important factors that can impact equipment reliability. By monitoring these factors, you can make adjustments as needed to help ensure optimal equipment performance. For example, if a piece of equipment is running too hot, it may be necessary to adjust the cooling system, check the lubricant, or make other changes to prevent the equipment from overheating. Similarly, if the equipment is vibrating excessively, it may be necessary to check for loose bolts or other issues that could cause damage. By monitoring these and other factors, you can make adjustments as needed to help improve equipment reliability and catch potential problems earlier. While many forms of condition monitoring involve sensors, you can still benefit from inspections and manual condition monitoring if you don’t have the budget for condition-monitoring technology.
Properly Secure Electrical and Instrument Panels
Even if technicians are regularly working on electrical and instrument panels, you shouldn’t leave them open or loose. When you don’t properly seal the panel doors, you are leaving them open to more problems. This is because dust, dirt, and moisture can easily compromise the life of every component in the panel. However, don’t just go around and close all the panels that have been left open. First, clean them with a vacuum brush and inspect the door gaskets for repair or replacement. Then, you can properly close the panels.
Clean Equipment Motors
Keeping your motors clean is an excellent and easy way to prevent them from overheating and negatively impacting equipment reliability. Electrical motors are not intended to be operated while covered in debris, product buildup, or other contaminants on the fan guard and motor fins. The buildup prevents the motor from cooling-off while it is running, which causes the insulation to break down in the motor. Walk about your site to clean the motors with a wire brush and give them some fresh, cool air.
Check the Foundations of Your Equipment
Improving your foundational elements is another easy way to improve equipment reliability. Take a look at the rotating equipment (fans, blowers, and pumps) at your site and write a list of those that have the following problems:
- Foundations are not sufficient or are not present – The foundation for rotating assets should be 3 to 6 times their mass.
- An extremely damaged or cracked foundation – This leads to loose or severely vibrating rotating equipment.
- Visually out-of-alignment rotating equipment – If possible, fix these first because if you can see it, it’s a real problem!
A lot of these locations will appear on the list of bad actors from the data collection step if you make a list of these items and compare them.
Update Your Drawings
A current set of drawings to work from should always be available to maintenance staff. Any time you alter equipment, the drawing must be updated and adjusted. Your organization likely has a management of change (MOC) process in place for managing your equipment drawings. Learn that procedure now, then start upgrading the designs for your most important assets. Since accurate drawings make troubleshooting easier and decrease the possibility of additional errors and mishaps, they will always cut down on the MTTR (Mean Time to Repair).
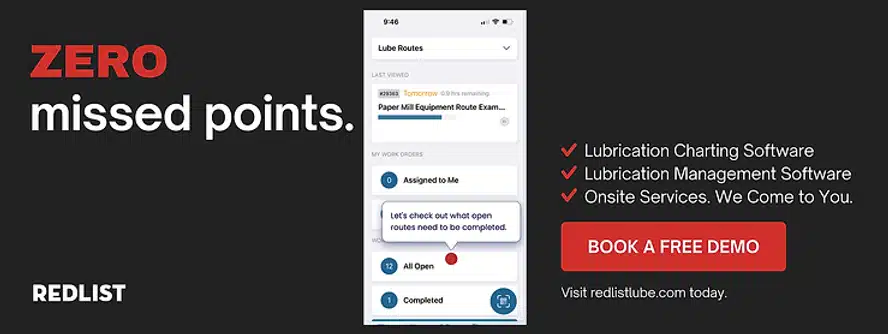
Improving Equipment Reliability Takes Daily Effort
No one ever wants to think about their equipment breaking down, but the fact is that it happens—sometimes at the worst possible time. By being proactive and taking a few simple steps, you can help improve your equipment’s reliability and reduce the chances of a costly breakdown.